LEADER PROFILE
John Malmgreen, Vice President of Manufacturing & Quality, Eastern Alloys | With HV Mfg Staff
Good Chemistry
HV Mfg travelled to Maybrook, Orange County, to sit down with John Malmgreen, Vice President of Manufacturing and Quality at Eastern Alloys. We spoke with John about the challenges and opportunities facing Eastern Alloys – and the manufacturing sector in general – as well as the career path he took to his current position and his thoughts on management and leadership. We also got a thorough chemistry lesson focused on the properties of zinc and aluminum alloys – a lesson that left us fascinated and wishing we had paid a bit more attention in high school chemistry class.
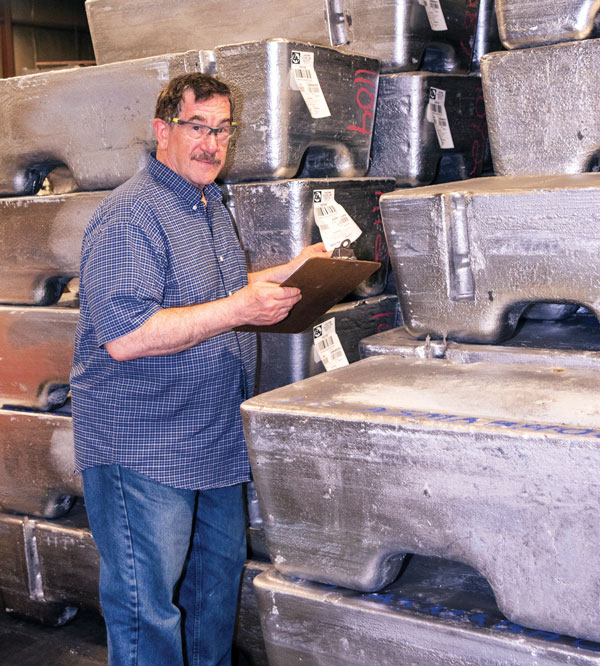
HV Mfg: Thanks for doing this. Let me jump right in. Where are you from and how did you get started in the manufacturing sector?
JM: Well, I grew up in Brooklyn. And as far as manufacturing goes – I’m not exactly sure how that happened! When I grew up there was never any discussion or exposure to industry either in my home or at my school. My father worked as a mechanic in the Brooklyn shipyards and after he married my mom he worked as a building superintendent while my mom was a bookkeeper/secretary for a printer. There just was no discussion about manufacturing, although I spent time with my father doing maintenance work in the building.
Later, when I was in the last years of high school and early years of college, my father became a partner in an auto salvage yard where I got great experience taking parts out of cars and seeing how they worked literally from the ground up. I suppose that these experiences would later help me when I did go into industry. However, I was a pretty good student and teaching seemed like a good profession for me so that is the direction I headed in.
My first job out of college was as a science and math teacher at a Catholic center for young women addicted to drugs. Father Daniel Egan – famously known as the “Junkie Priest” – hired me to teach math and science at New Hope Manor at Graymoor. Father Egan didn’t want the girls who were recovering to fall behind in their studies while they were at the center, so he hired a few teachers to keep them at grade level.
I taught all different levels and disciplines – the girls were all different ages. It was like a one room schoolhouse. It was very challenging. After a year or so I took a job as a ninth-grade science teacher in Monticello. I worked there about a year. I didn’t hate it, but I didn’t love it either. I think I expected the kids to be more self-motivated. And, then realized that teaching as a profession was not for me. I decided to start looking for something different, something more in line with my interest in science and chemistry.
I found a job with International Nickel at the research facility in Sterling Forest as a chemical technician practicing wet chemistry.
HV Mfg: Let me back up a bit, where did you go to college?
JM: I graduated from Hunter College, part of the City University of New York in Manhattan. I graduated in 1973.
HV Mfg: So, your first job in manufacturing was with International Nickel? And what exactly is wet chemistry?
JM: Yes, that was my first job in manufacturing. Wet chemistry is generally done, as the name implies, in the liquid phase, it is basically what you think of when you think of chemistry, test tubes, beakers, and burets on a bench being carefully measured and mixed together. Think of Sherlock Holmes at work in his lab in an old movie. In my position at International Nickel, I was using these methods to determine the purity of metals and the composition of novel alloys that were being developed.
Wet chemistry is really labor intensive but, I really liked the job and learned a lot. I also learned that I was good at it and while working at International Nickel I was able to get my master’s degree in chemistry from Farleigh Dickenson in New Jersey.
HV Mfg: Was there anyone at International Nickel who helped you along this path?
JM: Yes, absolutely. Bob Liu was my boss and ran the Wet lab in Sterling Forest for International Nickel. He was brilliant. So knowledgeable and experienced. No matter what we needed to test for he always knew the answer. “Mix this, add that, then this, wait 2 days then add this and test for that.” He was always right, and my only challenge was to try to remember or write down all the steps and later understand what chemical reactions were involved. I like to think that some of that knowledge rubbed off on me.
HV Mfg: How did you end up at Eastern Alloys?
JM: I had hit a bit of a dead end at International Nickel. I was working as a lab tech there and once I finished my master’s degree I was looking for something a bit more challenging. I answered an ad for a Chemist/Process Engineer here at Eastern Alloys. I came up to Maybrook to interview, and when I met Mr. Bauer, I knew it was a good fit. That was in 1978 and I have been here in a variety of roles ever since.
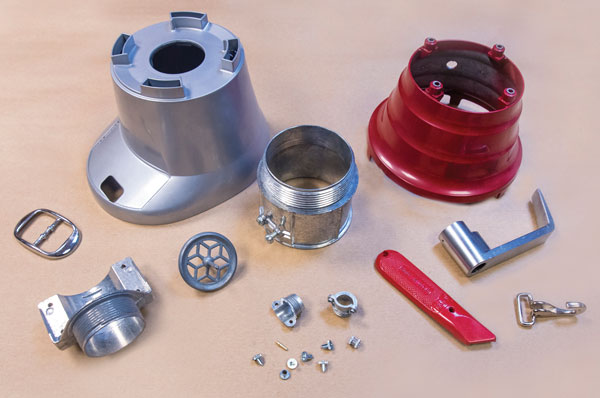
HV Mfg: We have had the pleasure of meeting Richard Bauer.
JM: Then you know that he is a great man and brilliant metallurgist, also great to work for. Eastern Alloys has been a leader in the zinc alloys industry for more than half a century and Dick, and now his son (also a metallurgist) and granddaughter, are the reason for that. They are very committed to – not just their employees and their customers, but also the zinc alloy industry as a whole. They, we, firmly believe that if we lift the industry, we will lift up Eastern Alloys.
HV Mfg: Now may be a good time for you to tell us about Eastern Alloys and the Industry. What do you make? How is it used? Who are your customers?
JM: “Eastern Alloys manufactures world-class zinc alloys for the die casting, foundry, and steel coating industries.” That is what the website says. It is pretty concise. But let me go a little deeper. Diecasting is a very efficient way to mass produce metal parts. Basically, you force liquid metal into a mold to make a part. It is used to make complex shapes, parts can be mass produced very precisely, and die cast parts are also very durable.
Some of our customers make tools, hardware, parts for the auto industry, and many more. You need to select the right metal for die casting a part to work. It needs to have the right strength and the right melting point. It needs to flow a certain way. Zinc, in some combination with other metals, is almost always the right choice.
Zinc alloys are also used to protect metals from corrosion. Steel will not corrode as quickly when covered with a zinc coating, even when a scratch or cut exposes the steel to air or moisture. The zinc coating will always tarnish and corrode first because zinc is more electronegative (more reactive) than steel and therefore provides cathodic protection.
Eastern Alloys’ customers depend on us to know about zinc die casting and zinc alloys for coating metals to help them succeed.
HV Mfg: Do you work with customers to help them find solutions? Do you develop your own solutions?
JM: Yes, and yes. We have some technical salespeople who are very knowledgeable about our alloys and capabilities, so if a customer is having challenges with a part or wants to improve its properties, we will work with them to find a solution.
We also are always working to improve the quality and versatility of our metals so that die casting is a more economical and practical manufacturing solution. I mentioned earlier that we are committed to the industry. That means finding ways to keep costs down and quality and productivity up for our customers.
HV Mfg: We can see why quality is so important and that determining the quality of your product is largely a chemical process. Is it still a very labor-intensive process?
JM: Quality is the core of our business and no, it is not as labor intensive in 2021 – there have been huge technological advances since my wet chemistry days – but we still rely heavily on smart, reliable people to run tests, calibrate equipment, and to interpret and document results.
Tests that used to take days to run now can be done in minutes. We use spark-atomic emission testing. We take a sample of our metal alloy and the machine fires a high voltage spark into the metal to create an energized cloud of atoms. The light emitted is measured to determine the various materials in the metal. Each element has a unique pattern of emission lines. By picking the right line and measuring the amount of “light” (typically UV), you can determine the concentration of the element. This is done simultaneously for each of the metal elements of interest.
The machine does a lot of work quickly, but it is only as accurate as we calibrate it, so we have strict procedures and benchmarks to keep it accurate.
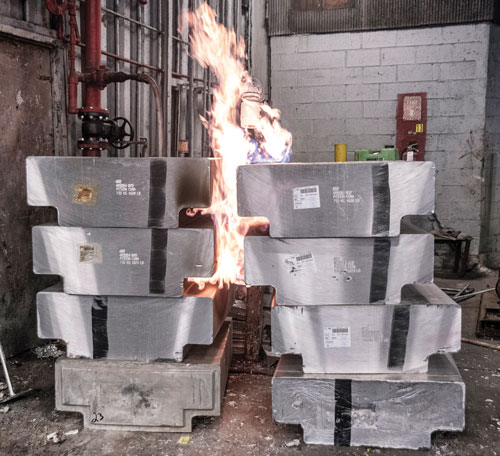
HV Mfg: You were hired as a Quality and Process Engineer and are now Vice President of Manufacturing and Quality. Were there any other titles along the way? What has changed in 43 years?
JM: I had the title of plant manager for big chunk of that time as well.
A lot has changed… and at the same time a lot remains the same. Technology has changed. We are way more efficient and productive than we were in the past because of technological improvements. We produce more here with fewer people. The quality and variety of our products have also changed and improved over time. The industry has changed, both ours and our customers. We used to, for example, sell much more to firms that made parts for the auto industry but as fuel efficiency became more important heavy die cast parts have been replaced by lighter materials.
On the other hand, we see opportunities in the EV market. What is the same is that I really like what I do and the people I do it with. The Bauer family’s commitment to the company and the industry is the same as it was when I first came on board in 1978. We are still focused on the customer, and I am sure that will not will change long after I leave.
HV Mfg: We understand that may be soon, that you are phasing out of the job – heading toward retirement. Is that the case?
JM: Yes, that is true. I am down to 3 days per week now and intend to be on a lighter schedule soon. I am developing my replacements. Andre Santa will be the Director of Quality and Kent Findley will be the Plant Manager.
What makes a good leader? Effectively communicating and setting clear expectations.
HV Mfg: Tell us about your leadership style and what do you think makes a good leader?
JM: I guess my style comes from my teaching days. I try to provide our team with all the information and tools they need to do the job and then trust them to do it. I try to communicate expectations and, for the most part, I am not disappointed. Of course, it is easy when you have a team like mine that are eager, willing, and motivated.
As far as what makes a good leader, I guess it is just that. Effectively communicating and setting clear expectations.
HV Mfg: Are there any mentors you had who helped you become an effective leader? Anyone from history you admire?
JM: I am sure there are historical examples, but none jump out at me today. I would like to again mention Richard Bauer. His commitment to the company, its customers and employees has been something I have tried to emulate during my time here.
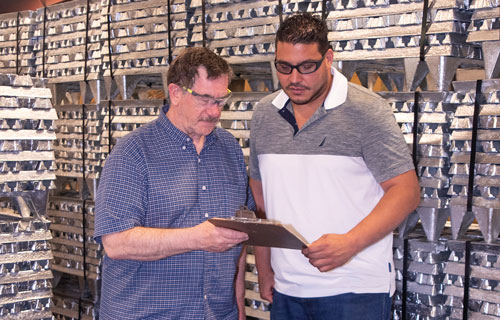
HV Mfg: What are some of the Challenges and Opportunities facing Eastern Alloys?
JM: As far as the challenges, the number one current issue is getting material. It’s hard to source metals and even harder and more expensive to get them trucked here. Longer term challenges are customers seeking cheaper solutions off-shore – die casting has been trending that way for years.
As for opportunities, I think we can continue to find new applications for zinc. It is not a particularly sexy metal, however is has some very useful properties and can be very competitive with plastics in many applications. In fact, we have developed a proprietary alloy that we have been marketing for several years. It is strong and can also be cast in very thin sections to make light but strong components.
HV Mfg: Any particular challenges being located in New York State?
JM: Energy costs are a challenge – it takes a lot of energy to melt metal – even zinc and aluminum. Trucking costs are high, and taxes and regulations are costly as well. We have a plant in Kentucky, so it is easy to compare the cost side of the business. At least relative to Kentucky, New York is expensive.
HV Mfg: You served as Chairman of the Council of Industry Board of Directors and have sat on our Board for more than a few years. How has Council membership been beneficial to you and Eastern Alloys?
JM: I have found being connected to other manufacturers in the region to be very helpful. It is a great network. We have also had several people complete the Certificate in Manufacturing leadership and that has been very valuable.
We also buy our energy through the Council’s buying consortium and that has saved us a lot of money and time through the years.
HV Mfg: Thank you very much for your time – we really enjoyed the interview and the chemistry lesson.
JM: My pleasure, thank you for the opportunity.