COUNCIL OF INDUSTRY STAFF | BY CLAIRE LIEBOWITZ
THE FACTORY OF THE FUTURE IS DIGITAL.
Are you ready for the transformation?
Manufacturing is entering a new age, which is brought on by the advancements in digital manufacturing software, allowing creators to take their innovation to a whole new level.
“Digital manufacturing design is not just a small incremental improvement in the industry, it’s a breakthrough improvement. It’s a revolution.”
Sri Vilayanoor, CEO of Ignition Life Solutions
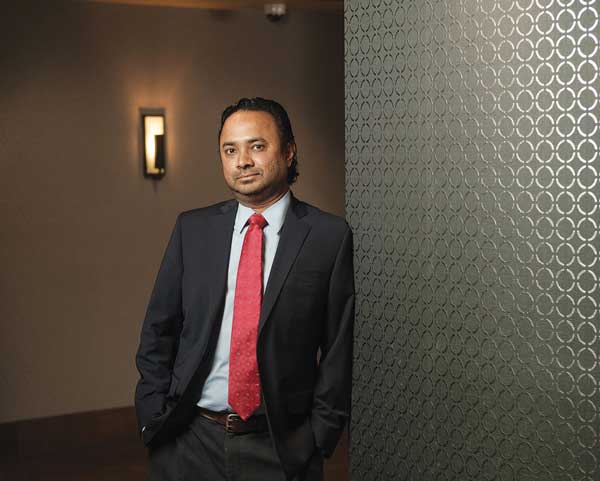
Most experts agree that digital manufacturing is the use of technology to increase efficiency and productivity to meet customer needs.
Importantly, this application of technology does not mean replacing workers by automating the assembly line to cut costs for a company. Instead, it is the use of information systems programs that enable a manufacturer to create an incredibly wide range of products and services with a higher quality while also providing the ability to make quick changes to the product as consumer market demands also change. The goal is to augment the already existing process of manufacturing.
Digital manufacturing includes, but is not limited to, data analysis software, simulation, eCommerce, Artificial Intelligence (AI) and the Industrial Internet of Things (IIoT), robots, sensors, and automation. Companies implement these technologies in order to help their workers by making the job easier and quicker to accomplish without any additional strain on the labor force. “There’s an explosion of complexity happening in the industry.” Fram Akiki, President of Joun Technologies said. “The product has become more complex, there’s complexity in the supply chain, complexity in the customers.” Digital transformation can help manufacturing companies to gain a competitive advantage by providing means of adaptation to the increased complexity of the market.
“The idea of trying to bring in technology-based change into a manufacturing environment is extremely daunting, but there is an absolute need to do it.” Akiki said.
Now is the prime time for promoting it as the future of manufacturing. Naturally, before diving into any big change, manufacturers have some reservations about this new manufacturing era. This is why Akiki, Vilayanoor, and other consultants and educators are working to familiarize the workforce with digital transformation to provide a smooth sailing transition into the future.
The digitalization of the manufacturing industry has become so popular, it’s almost a necessity for companies. Consultants are advocating for it by promoting the future of manufacturing, providing examples of how manufacturers are using it today, and even working with academic organizations to prepare the incoming workforce.
HISTORY OF MANUFACTURING
Digital manufacturing is still relatively new because of its dependency on IT and CAD software. The ability to operate multiple programs from a single PC and give precise directions to a robot is increasing every day with the hard work of engineers and software designers. But it didn’t start out that way.
Between the late 1700s and the early 1800s, America went through its First Industrial Revolution, which signified the transition between craft production process and the use of machinery powered by water and steam. This resulted in changes in the textile, iron, and mining industries with the introduction of more complex factories.
The Second Industrial Revolution, or the Technical Revolution, occurred between 1871-1914. Along with it came higher speed electricity, railroads, and telegraph networks. Which happened just in time for the start of World War I, during which fast travel and communication was of key importance.
The Third Industrial Revolution of the late 20th century is known as the Digital Revolution. The inventions of this industry were not as visibly in-your-face as factories or trains. This era saw the invention of the super computer, and eventually the PC, which increased the speed of communication, as well as advancements in manufacturing processes. Most importantly, the digital revolution brought forward the rise of the internet and IT.
INDUSTRY 4.0
Industry 4.0 is just coming into being and has been dubbed the Imagination Age for its focus on creativity and originality, rather than analysis of the years that came before. However, it is this analysis and IT processes that allow for innovation and creativity to take the front seat. Industry 4.0 can be compared to the evolution of smartphones; we are entering an era of smart factories.
There are several trends that are growing in popularity in this newest revolution that all serve to make the manufacturing process more efficient. Automation, for example, is the use of robotic sensors and other automatic measuring tools that are connected to software that provides data analysis to enhance decision making. In an age where customers value customizations and personalizations of products, the capability of many rapid, profitable decisions in a short period of time is essential.
Big data is the root of what needs to be analyzed with the help of technology such as automation. Big data refers to the sheer amount of data that has become too complex to be processed by traditional means. It can be divided into three subcategories: volume, velocity, and variety.
Also known as the 3Vs, as Vilayanoor fondly calls them. Manufacturers collect huge amounts of data from industrial equipment to social media every day. Maintaining and storing all that information requires an overwhelming amount of data storage and gets costly very quickly. Not only is a lot of data being recorded, but it all happens at a very fast speed. Advancements in the internet and IoT allow information sharing to become faster and faster, overwhelming software of the digital revolution. All of this can’t be done today, which is why information management systems of Industry 4.0 will be able to process big data at the click of a button. The faster the data analysis, the faster the product life cycle.
DIGITAL TRANSFORMATION IN PRACTICE
Digital manufacturing is particularly useful in collecting data from the consumer market. Vilayanoor’s go-to example is the smartphone industry, Smart phones are able to collect field data from their customers to determine what about the product is and isn’t working, and what the customers do and don’t like. This allows smartphone companies to come out with newer models in a shorter amount of time with a greater sense of security regarding the customer reaction than in the late 2000s and early 2010s.
Apple is a very clear example of this. There was only a ten month gap between the iPhone 12 and the iPhone 13. After analyzing field data, Apple Inc. was able to determine that customers liked the iPhone 12 Mini option rather than a phone slightly too large to fit a pant pocket. So they created an iPhone 13 Mini option along with the standard iPhone 13. Field data also showed the importance of a high quality camera. Today, these phone cameras are so advanced, it can be hard to determine if a photo came from a phone, or a high-quality multi-thousanddollar camera used by professional photographers.
Field data is not only used to improve physical aspects of a product, but operating systems as well. Microsoft Windows is a computer operating system. Every time a new version is released to the public, a slightly updated version is released a few months later with small fixes to correct bugs or complaints customers have had about the operating system. Windows 11 was just made available to Microsoft users, meaning in the next few months, a slightly updated version will come out that will run a little smoother and faster. The collection and analysis of data made available by digitizing the manufacturing process is what allows for companies to adhere to customer demands with a relatively quick response time. As Industry 4.0 continues to develop, updates will be coming out with greater regularity.
Most manufacturing companies are successful because they work in tandem with other companies in the industry, whether they are shipping companies or other manufacturing businesses. The data and information sharing systems in place today between companies result in a huge waste of materials, which is known as the bullwhip effect. The bullwhip effect occurs when there is an increase in demand that suppliers must meet in order to keep their customers happy. Distributors begin this process by increasing their supply orders. One product is made of several parts, all of which have to be made, and then manufactured along the supply chain until the result is the final product. When each tier of the supply chain over-orders materials from their suppliers, the bullwhip effect grows exponentially, creating a significant waste in materials, time, and money.
According to Vilayanoor, the goal of Industry 4.0 is instant data transfer, which will help to reduce the bullwhip effect by allowing every part of the supply chain to be on the same page. This advanced communicative technology allows for every party involved to know what the end result is, and if that result changes, how everyone will accommodate accordingly. It explains the need for the fourth industrial revolution; to achieve the greatest potential of all resources used in the supply life cycle.
IT’S ALL ABOUT PEOPLE
Industry 4.0 is more than a little change in the Product Life Cycle (PLC); Vilayanoor said it’s a reimagining of the PLC, resulting in a continually evolving System Life Cycle (SLC) perspective. Understandably, executives are weary of change and the payoff of implementing a brand new system. Clarkson University is one of many organizations ready to embrace the change and prepare the future of the industrial labor force.
Professors at Clarkson understand that engineers are only a part of the manufacturing equation. Collaboration between management and engineering teams is necessary for optimal effectiveness.
Clarkson prepares its students to be flexible and welcome change by understanding all aspects of the industry, not just their specific field.
The Clarkson administration does this by designing flexible classes that incorporate the perspective of field experts and what the industry needs.
THE IDEAL WORKER
Luckily, for these new college grads, companies are broadening their search for new employees. “There’s such a labor shortage that if you start putting in these ‘must haves’, your search becomes very long and there’s not many available candidates,” Neil McGill Director of Operations at Allendale Machinery Systems said. “The companies that are growing the most are the ones who realize they have to start looking outside the normal labor pool and build internally.”
Fluidity is the future of manufacturing and the digital transformation. Manufacturers and their employees who allow themselves to be malleable and open to new ideas are going to take over the competition. Educators and consultants alike agree that flexibility is essential for success in the digital transformation age. Technology provides the means necessary to turn ideas into reality; adapting to changing manufacturing technologies ensures the possibilities of the future to become the present.
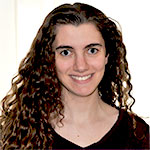